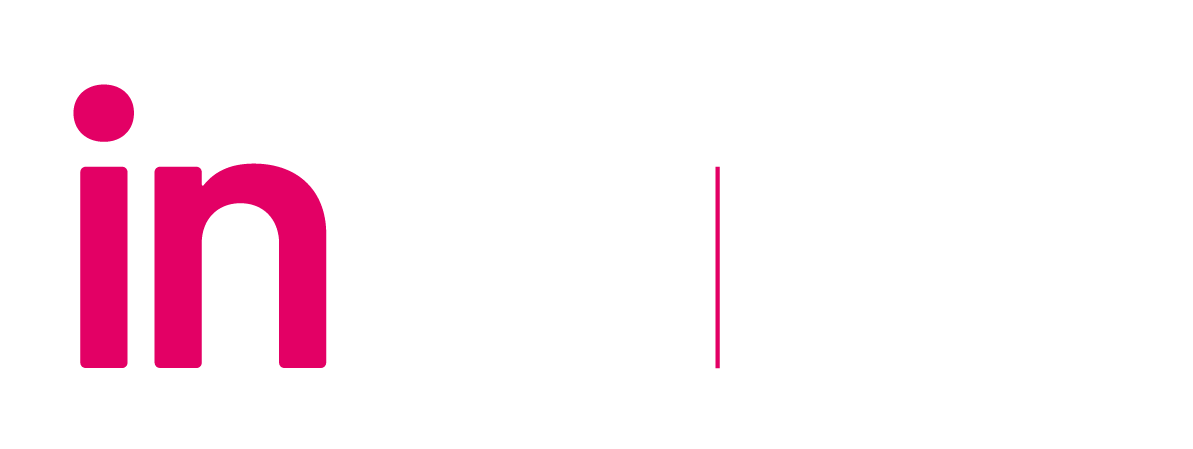
Office Hours
Mon to Fri: 9:00am to 6:00pm
Sat, Sun and Public Holidays: Closed
Mon to Fri: 9:00am to 6:00pm
Sat, Sun and Public Holidays: Closed
Singapore:
55B Temple Street
Singapore 058600
Singapore 058600

cs@inft.co

(+65) 6635 5668
What we see on the shelves of the grocery stores and the services we receive at the customer service centre are the result of a long drawn, established process. Through the supply chain management process, products and services move through the supply chain to transform from mere raw materials or skill sets into finished products or packages that consumers demand.
The supply chain consists of a series of steps that bring products and services closer to consumers’ doorsteps.
Those in the supply chain circle are producers of raw materials, vendors, manufacturers, developers, designers, warehouses, transportation and shipping companies, distribution centres, marketers, and retailers.
At each point of the supply chain, there are challenges to overcome and if there is a disruption, the entire supply chain is affected. One example would be the grand-scale disruption to the world's supply chain last year.
Despite the traditional supply chain’s long-established efficiency, it is difficult to manage even without disruptions. The supply chain was quickly affected by soaring shipping costs, shortage of manpower, port blockages and lockdowns, pandemic restrictions, long cargo wait times, and sudden stockpiling of supplies.
As the economy tries to reach its pre-pandemic efficacy, the struggle to keep up is real. Companies have grounded themselves in decades of discipline in creating a 'just-in-time' supply chain that responds to market demands as is.
Moving forward, here are some of the challenges we may face in the future.
The importance of good customer service in the supply chain is not always immediately apparent to those who are NOT in the circle. It is one of the most critical points of management and ensures that the right number of products or the right kind of services reach the right people.
Without good customer service, sales and marketing teams, decision-makers will find it difficult to respond to the demands of customers. The direct feedback is crucial to a functioning business.
It is from the customer service team that a company gets to hear from the customer. Knowing the data and pain points directly from clients will help oil the engine of the supply chain.
Logistics and supply chain management are intertwined components. With the sudden stress of change on supply chain infrastructure and management, shipping and transportation companies are under a lot of pressure.
Some of the ways a company can improve its customer service include:
Wall Street Journal reports that business logistics rose by 22% in 2021; the world continues to seek out a balance between meeting consumer demands and controlling expenditure. Disruptions to the supply chain are costly, with the world forking an average of 184 million per year.
The cost of procuring and securing affordable, quality raw materials, energy, labour, and shipping, has risen and fallen. Operations and management everywhere had to shift the way things worked to continue providing quality products and services without hiking up consumer expenses.
Nobody has found the right answer at the point of writing. We don’t know when the cost of freight will return to normal or should we be more prepared for future delivery disruptions. But experts continue to experience financial loss due to persistent transportation delays, warehousing and inventory management inefficiencies, and high freight costs.
Before the pandemic, companies have come to count on the reliability of the established supply chain management system. We have to, however, realise that risk management should no longer be just an afterthought. The reason for complacency was that the supply chain had, before the pandemic, experienced only very sporadic conflict or disruption. The cost, therefore, was negligible.
But the recent years saw widespread shortages and delays, blocked canals, winter storms, and grounded container ships that threw the supply chain off its centre. The events served as reminders of how vulnerable the system is; we need a more secure and resilient alternative to routes and suppliers.
As most of the risks related to the supply chain fall under the four main categories of economic, environmental, political, and ethical disruptions, companies are now looking to move into basic supply chain mapping.
How successful it will be and how long it will take remains to be seen.
Only in hindsight, do we see that we have stopped building solid networks of suppliers, or creating alternative shipping options. We've stopped the growth of the supply chains.
It is an investment in having a more mutual understanding and beneficial relationship with your business partner. This has always been the bedrock and foundation of long-lasting traditional business models. Because of contentment and industry-based pacing, there is no longer a desire to change how things work.
Companies must view their network of contacts as previous and continue to build better networks. The relationship customers have with their current, past, and future suppliers, manufacturers, distributors, or wholesalers will give the company a more stable foundation to fall back on if anything untoward were to happen.
The demand for container shipping rose considerably during the pandemic as sales on eCommerce sites soared. And as countries faced lockdown measures, the need for raw materials and consumer products grew correspondingly.
The capacity did not meet demand, hence, the price of shipping spiked last year. As of 2021, freight prices from China jumped 240%. When the demand cannot be forecasted, it leaves companies without a guide as to how much inventory to stock up on, manufacture, or distribute.
One good example was the jump in demand for face masks and hand sanitisers during the pandemic. By the time we needed a large supply of them, especially a product so specific, it shattered predictions.
When it comes to such a non-internet-based challenge, digital transformation can be tricky. However, technology quickly helped solve a number of potential problems related to port congestion, manpower shortages, and even inventory management.
There is, however, a need to change the way we think about traditional supply chains. Usage of drones, robots, artificial intelligence, electric vehicles, on-demand delivery, and cloud computing are already in discussion and being tested in stages.
Although some of these systems are cost-effective when implemented in specific departments, e.g. digital transactions and eCommerce, the challenge lies in implementing a system that works across the entire supply chain. It takes time, money, and alignment across the organisation and industry in order for the magic to happen. For example, a company may not be accustomed to work with multiple warehouses or will need time to get used to omnichannel selling and fulfilment.
As mentioned, these things will improve over time as changes take place across the distribution network. As demand forecasting becomes more agile, cloud-based, and predictable, the supply chain will continue to grow and evolve along with consumer demands.
If you are looking for a neobank in Singapore to help you adapt to changes to the supply chain, we have flexible SME funding for your business right here. With our digital business model, you can perform international business and accounting completely online using one dashboard. On top of that, INFT business financing will help you during the transformation process.
Signing up for an account with INFT is absolutely free! You can then learn more about our Cashline offering, Invoice Management platform, and use our Global Payment feature to receive and pay anyone, anywhere!
Don't forget to sign up for our newsletter for business advice, tips, news, and also updates and promos.